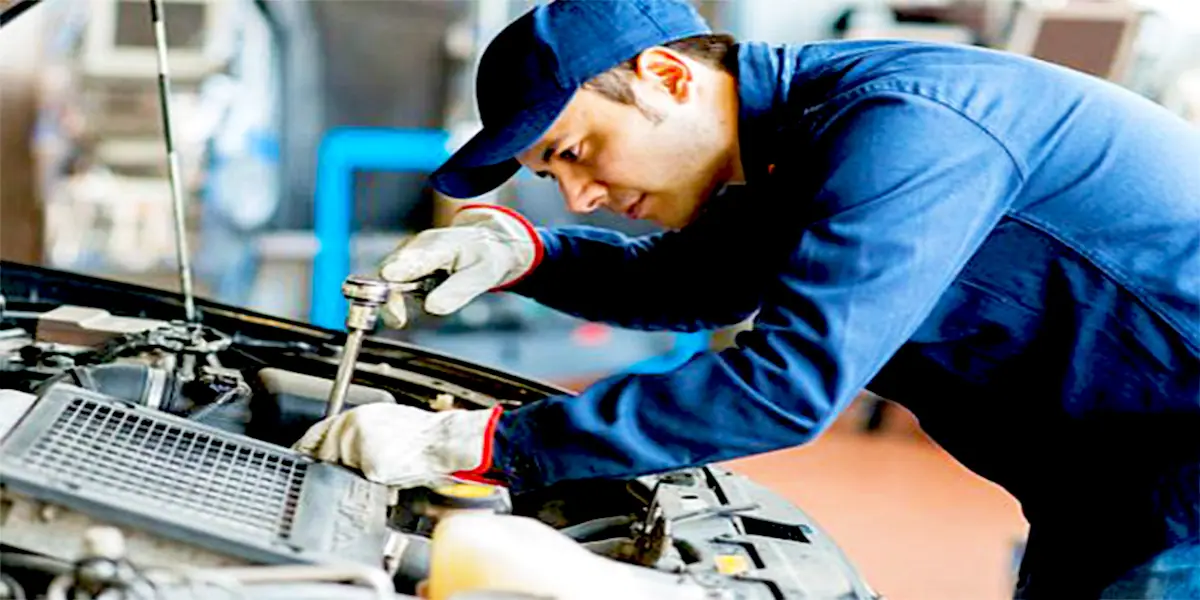
5 Common Preventative Maintenance Mistakes You May Be Making With Your Fleet
Category: Product Support
Continual maintenance of your fleet plays a vital role in ensuring optimal operating conditions for your equipment. While many fleet owners recognize the importance of maintenance, some aspects still get overlooked.
Putting off an oil change one day or forgetting to check the service light may not seem detrimental at the moment, but avoiding maintenance can lead to further damages in the long run and may even affect the uptime of your company.
Maintenance Errors and How To Avoid Them
Truck preventive maintenance mistakes are often not intentional but can hurt your fleet in more ways than one. Here’s what you need to know about common truck maintenance problems and how to avoid them.
No Standards for Scheduled Maintenance Programs
Many fleet owners have set standard intervals for maintenance programs, but not everyone sticks to the schedule. Fleets used 24/7 require preventive maintenance, but when you put off a brake check or oil change, more damage will occur.
If your machines go too long without being checked, your repair costs can also increase and hurt your fleet in the long run. Neglecting routine maintenance can lead to severe problems. To avoid future issues, get your equipment inspected at scheduled times with no excuses.
Looking at Your Fleet as the Same Equipment
Fleets have several different pieces of machinery, ranging from bulldozers and forklifts to tractors and skid loaders. However, if you look your fleet thinking everything has the same problems, you’re doing it wrong. Different vehicles require different interval maintenance schedules. By treating and maintaining each piece of individual equipment, you can avoid this one common truck maintenance problem.
Not Capturing Data From Inspections
Fleet owners often don’t take into account the information they get after inspection. When you don’t capture the right data, you miss out on valuable insights to problems across different makes and models in your fleet. You can use the data to determine which systems are failing can develop a game plan on how to address specific issues.
Not Training Your Drivers
Truck preventive maintenance problems can arise when your drivers don’t understand the
difference between fault codes that need attention or don’t. When a warning light appears on their dash, a driver should take note and have the problem resolved. While some lights indicate a faulty sensor, workers should know when to take action and when to hold off on going to the maintenance shop. If they neglect the wrong lights, it can lead to serious damage.
Looking at Your Fleet as Tools Instead of Assets
Another truck maintenance mistake is seeing your entire fleet as a tool instead of an asset making you money. If you use equipment too hard and don’t maintain your trucks, they can fail, break down and cost you money. If you take care of your equipment, it will result in well-maintained trucks for increased production.
Why It’s Important to Prevent Issues
The purpose of a scheduled maintenance program is to have your fleet experience zero breakdowns. Inspections now and no failures later mean the schedules pay for themselves. Mechanics can prioritize and determine what needs fixing right away. The goal is to get your fleet on a maintenance program to keep equipment operating safely and to avoid interruptions.
Truck Prevention Maintenance at NMC
Even though there are many common truck preventive maintenance problems that can occur, our mechanics find problems early. Our technicians strive to clean and repair your machinery rather than replace it. NMC preventive maintenance includes brakes and wheels, clutches and fluid power, and suspension steering and transmission.
Explore NMC’s related services for truck preventive maintenance services or contact a representative to schedule a service. You can also call 800-628-6025 for more information.